A Promotion for Reduction
As we recently began exploring, the journey to “net zero” is a complicated but essential one, and one that encompasses many angles, not just decarbonising. Whilst not entirely to blame for the existing issues, as an industry, design must play a key role in altering the ways in which we manufacture, transport, apply and use our materials and products. The threats created by climate change, along with the destabalising of ecosystems and plundering of natural resources are vast, so a move towards novel, perhaps even quite radical, ways of working may have to be the answer – and there are plenty of projects out there leading the way forward.
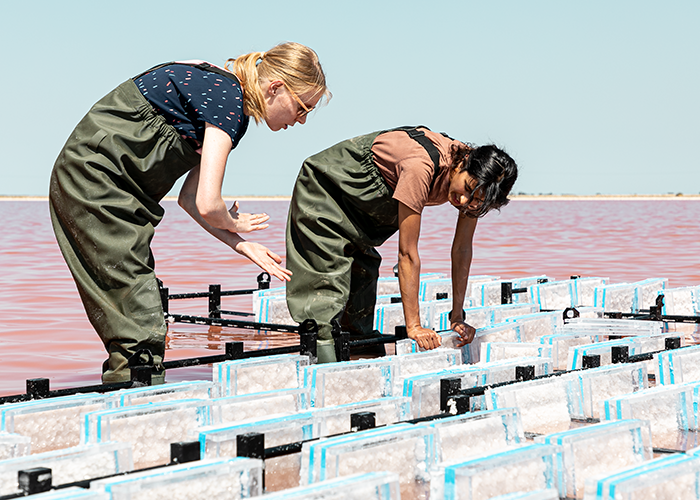
Photography by Adrian Deweerdt
Given the sheer volume of electronic consumables available on the market today, it’s no wonder that E-waste makes up a huge percentage of the annual waste that goes into landfill. Electronics have become a bedrock of 21st Century life, but the multi-layered nature of the materials required to make them work, as well as look and feel good, has made it very difficult for them to be recycled or reused in any way; until now that is.
Studio Plastique had been amassing a great volume of material research with the aim of recycling E-waste, but instead of trying to figure out how to repurpose entire devices, they focused upon one core component; glass screens. The project soon became a collaborative one, with trans-disciplanary practice Snøhetta joining in on the research and later, Italian ceramic tile manufacturer Fornace Brioni getting involved. Numerous tests and variations were carried out during the prototyping stage and it was this that led the team to be selective once again, this time realising that a natural application for their output would be glass tiles. As a result they honed in on some of the larger forms of E-waste glass via oven and microwave doors. With a decent supply of material and the expertise of Fornace Brioni, Common Sands – Forite was born.
The collaborative partnership is key to the project, not least because the aim is to turn this novel development into a scalable architectural solution. Glass of course plays a huge role in the design of many modern buildings and Common Sands – Forite now allows for alternative material choices when it comes to specifying. Whats more, the inherently recycled nature of the speckled, terrazzo-like aesthetic showcases the materials history and positive transformation within the surface, whilst also offering a viable solution when semi-transparency is required.
In some ways the opposite can be said of Carvey Ehren Maigue’s material invention, AuREUS. For whilst it is very much intended to cover the glass cladding of buildings, transparency is one of it’s defining features. That’s because the unique surface solution is a form of solar panel, although perhaps an even more attention grabbing characteristic is that it is made from agricultural waste. The project was developed by Maigue whilst studying engineering in the Philippines at a time when many crops had been devastated by typhoons and flooding as a result of climate change. As such the material offers a double-whammy for sustainability.
In 2020 the project won him the prestigious James Dyson Sustainability Award and that has led to teaming up with a global brand that are able to test the commercial scalability of the material. All being well, this will mean allow the clever technology of AuReus to be taken forward into mass production, meaning waste could be transformed into a surface that in turn transforms UV light into clean energy. What is further significant here is that ordinary solar panels require direct sunlight because they rely on visible light. The hope is that by extracting bioluminescent particles from fruits and vegetables and setting them in the fluorescent resin surface, whole glass buildings can become efficient and sustainable solar energy power stations in their own right.
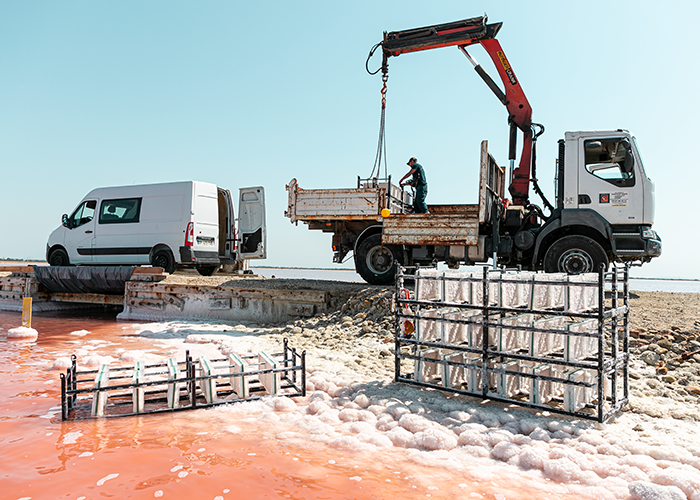
Photography by Adrian Deweerdt
Material innovation is a passion shared by the team at Atelier LUMA, a design and research lab located in Arles, France. Whats more, collaboration is once again central to their approach, with an ever expanding network of experts coming together to explore how local resources can be used to create material solutions that play a key role in positive ecological, economic, and social transition. One such recent project is The Crystalization Plant, which seeks to tap into the ancient process of producing salt in the neighbouring Camargue region:
“For centuries, the saltwater of the Rhône delta has been used to produce salt. Today, production is primarily destined for the agri-food and chemical industries. Since 2017, Atelier LUMA has been exploring the physical and aesthetic attributes of Camargue salt in order to develop materials that feature this local resource. This research opens the salt industry up to innovative applications in new fields, such as design and architecture.”
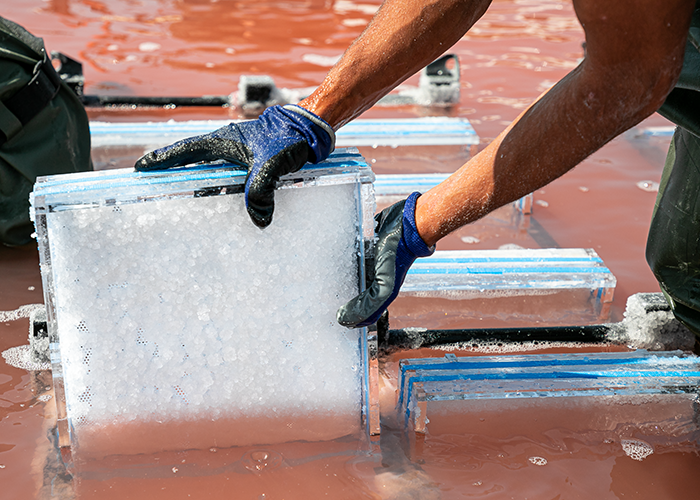
Photography by Adrian Deweerdt
Years of indepth research into the crystalization process has allowed designers Henna Burney and Karlijn Sibbel to perfect the process of growing salt crystals on metal mesh that is submerged in the Camargue salt flats. Alongside this, techniques including moulding, pressing and thermocompression have also been trialed with the aim of creating three-dimensional objects.
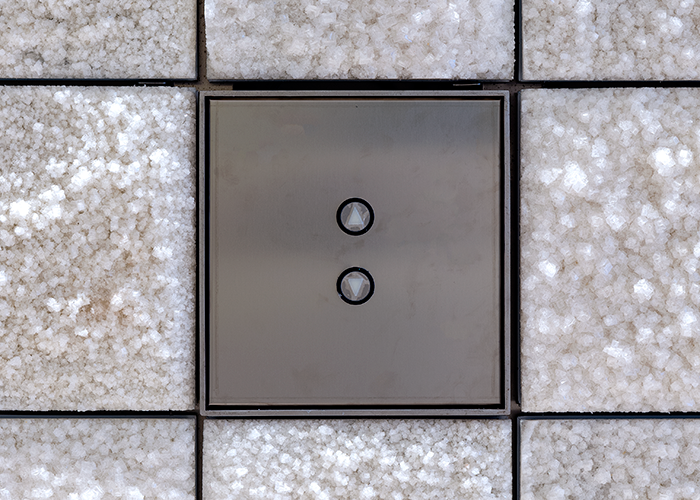
Photography by Adrian Deweerdt
These naturally formed surfaces not only have a low environmental impact, whilst being seemlessly integrated into the local topography during their production, but they are also viable surface applications for architectural settings. This is evident in the lobby of the local Frank Gehry designed Luma Arles arts centre. The towers exterior may be clad in curved metal shingles, but inside the walls are covered in the textured tiles made just down the road from salt.
Sometimes some of the most impactful innovations are the simplest ones and Danish furniture brand Takt’s decision to make all of their furniture flat packed is one that greatly reduces transport and packaging based emissions. That may not sound like a very novel idea, particularly to anyone who has bought IKEA furniture, but it’s all part of a larger vision that the company is rolling out across all facets of the business:
“We have worked intensively to create clarity in the climate footprint of each of our products. We have mapped the CO2e impact during the entire process from basic materials to production, shipping, daily use and the final disposal after many years of use. This way, you can see the composition of the climate footprint on each of our product pages.”
This approach advances the sustainability of the brand beyond simply using FSC-certified wood (which they do,) something that is further underlined by the fact that they’ve already signed up to the B Corp Net Zero 2030 pledge and are committed to achieve net-zero emissions before 2030. The result of all of this is that customers have a very real sense of the environmental impact, or lack thereof, that the beautiful furniture they’re assembling has; which in itself creates a deeper and more meaningful connection to the objects in our homes and places of work.
The materials and furniture we use to construct and decorate buildings play a huge role in the fight against climate change but of course, if we want to truely speed up the process of reducing carbon emissions and living in a more sustainable way we need to take a holistic approach to how we design spaces. Given that restauranter Douglas McMaster’s approach to the food production of Silo in Hackney Wick is to produce zero waste, it’s little wonder that the interior design follows suit.
Led by circular design specialists Nina +Co., the design of the space closes the loop in the same way that the food does, as Nina Woodcroft of Nina+Co. explains, “Following Silo’s post-industrial ethos, we opted to work with local crafts people using age-old techniques, as well as harnessing innovative materials and technologies” Those surfaces include a sumptuous all natural cork floor, bar made from recycled polyester waste with a Smile Plastics countertop and pendants made from myceliuem and seaweed, amongst other things.
This 360 approach to design is emulated in another more recent project by Nina+Co.; the first bricks and mortar store for eyewear brand MONC. The brief included the clause that the space is on an initial short-term lease, meaning adaptability must be taken into account for the sake of longevity. As such, many of the design elements have been created with moving on to another space in mind – or recycling or disassemble – although it’s the material choices once again that really stand out when it comes to a circular approach.
Once more, mycelium has been utilised, this time to create moveable plinths, along with hemp, layers of cornstarch foam and a big slab of apricot recycled plastic. MONC’s own material-led sustainable approach is also highlighted with accents of one of their primary materials for producing eyewear, bio-acetate, being used within the displays, thus underlining the companies own inherent use of biodegradable and petroleum-free materials.
This type of holistic approach to interior design is highly apparent in another recent restaurant re-design; Mo de Movimientoin in Madrid. Machado-Muñoz gallery commissioned designer Lucas Muñoz to carry out his largest project to date, and the result is something quite special. The brief asked that the project should “have the scope to re-define the traditions and techniques of architecture, design and consumption, within which, the creative and constructive process becomes part of the identity of Mo de Movimiento.”
It’s fair to say that a highly distinct visual identity has been produced, and one with which materials and systems have been rigorously researched and chosen for their sustainability credentials. This was made possible once again through collaboration, with Muñoz bringing in a sustainability team to help ethically and mathematically measure every material and strategic decision from the concpetion to completion of the project. Every facet of the design is teeming with detail, including benches made from the recycled rubble extracted during the building process, simple and effective seating made from reclaimed timber as well as uniquely reupholstered office chairs made up fro scraps that invite you to choose your favourite.
Overhead, recycled textile acoustic panels, used with as few cuts as possible to save on waste, hang above a modular metal mesh. This is used to hang lighting and the innovative adiabatic ventilation system, which takes traditional techniques of using terracotta vases and water to create a cooling effect.
Projects like these show that with time and lots of in-depth consideration, buildings can use effective materials and systems that make them truly sustainable whilst fostering deeper connections with their users.