Paul Jones Discusses Lean Manufacturing at Morgan
At a time when manufacturers are more acutely aware of finances than ever before we sat down with Paul Jones, General Manager at Morgan to discuss his approach to lean manufacturing and its potential impact on the bottom line, employee morale and customer satisfaction.
Find Morgan on Product Finder]
Please could you introduce yourself and your role at Morgan?
I’ve been Managing Director at Morgan since May 2021, though I’ve held a few different positions in my time here.
I first joined Morgan for an industrial placement in 1999, as part of a four-year course studying furniture production management. In my first role here, as a student engineer, I was encouraged by the management team to devise lean manufacturing processes, which I’ve continued to implement to this day. As part of that, I spent time in every single part of the business and was given free rein to suggest improvement projects.
After spending 11 years at Morgan as production manager, I stepped away for several years to broaden my experience before returning in 2019 as General Manager.
What is your background in ‘lean’ manufacturing and why is addressing this through your production at Morgan so important?
Lean manufacturing was a key part of my production management qualification, and eventually led me to design an award-winning Lean and Continuous Improvement Programme. Through spending time in every part of the company and being able to investigate and make recommendations quite freely, I quickly realised the benefits of lean and never looked back.
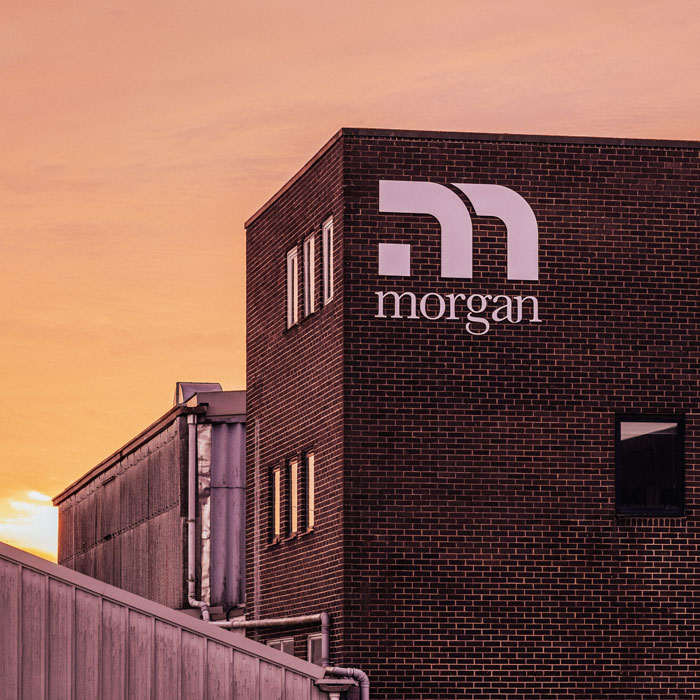
Photography by Taran Wilkhu
The biggest benefit is the empowerment and engagement with teams. Once people understand it will make their lives and processes easier, keep customers happy and ultimately generate more work, it develops a momentum of its own.
It’s win-win. At Morgan, we’re passionate about delighting our customers through everything we do, and lean is all about delivering value through the eyes of the customer. Lean principles keep us focused on what’s important. It doesn’t just impact our manufacturing. We’re on a company-wide sustainability journey, minimising non-value add processes and reducing or eliminating waste wherever possible.
Morgan recently launched their Lean Academy. Can you tell me more about the initiative’s objectives?
Rather than relying solely on department heads and the production manager to deliver on lean, we wanted to build a broader, recognised lean continuous improvement team. By offering all staff the opportunity to go through this five-stage formal training programme, we’re spreading key skills across the business, enabling it to run more optimally. The more people we have driving in the same direction, the greater chance we have of delighting our customers even more.
Development of the academy was, largely, a direct result of our open company culture. Our employee survey last year showed a demand for further learning, so we put the programme together. The team responded by wanting to be part of it and implementing it.
One of the impacts of lean manufacturing is successfully achieving high levels of on-time delivery. Have you reached your targets and how do you customers benefit?
As we speak, our tracking 12-month on-time delivery in full (OTDIF) is 99.5%. While I would say we’ve reached our target, we’re still always looking for new opportunities for improvement.
As for the benefit to customers, when we set a delivery date, it’s in our hands to be able to achieve it. We are in control of so much of the process. We start with trees, design in-house, manufacture in-house, work with as many UK supply chain partners as possible and handle deliveries ourselves.

Photography by Taran Wilkhu
Most of our customers are used to suppliers calling about delays or things gone wrong. We’re calling them about delays only 0.5% of the time, and this tends to be down to fabrics. When things do go wrong, our team will find a solution without impacting customers or the product. This is testament to our company culture and the success of our people being involved in lean principles.
How have you addressed sustainability through your manufacturing practises?
We’ve made myriad changes over the years, from adopting a Biomass boiler and a solar PV system to offering non-VOC finish options and minimising wastage through pre-cut foam. All our efforts to reduce our environmental impact have helped us achieve the highest ‘A’ level rating on our Energy Performance Certificate (EPC).
Broadly speaking, the key factor on our sustainability journey has been the unique way we manufacture. We don’t have a warehouse full of product we’re having shipped in and made in different parts of the country or beyond. We’re only consuming resource against specific customer demand. As an added benefit, by not having a warehouse full of stock we need to try to sell, our design team is free to move and innovate in whichever direction they want.
What is the next target you plan to work towards?
One of our next big targets is about connections with our industry. Our customers are busy people working on multiple projects. We want to ensure they understand our offering, what we can achieve and how it links to their sustainability drive and pain points, around lead times for example. There’s so much we’ve done and are doing with the customer’s challenges in mind, so we need to make sure they’re taking advantage of that.
One of those challenges right now is inflation. Our lean approach means that our 2023 price list includes some price reductions, with other collections seeing a maximum 7% increase.
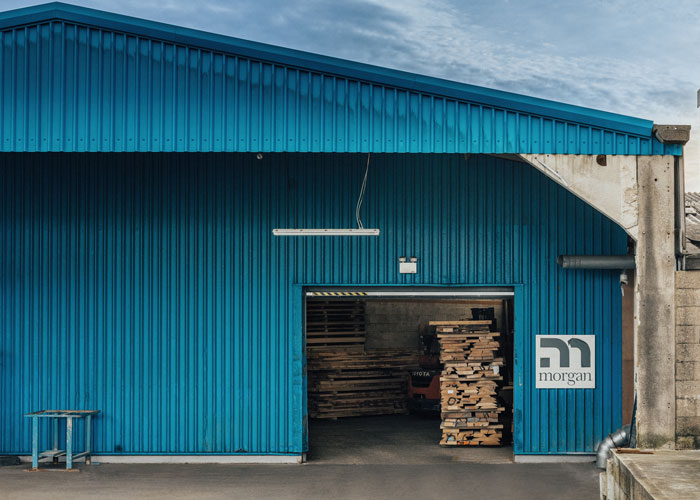
Photography by Taran Wilkhu
With so many suppliers to navigate, we need to help our customers remember that we manufacture everything in our Hampshire factory, we really do start with trees and we really can offer a two-week Quick Ship lead time.
Contact Morgan through Product Finder.
Product Finder is a unique search engine created especially for interior designers to source contract furnishing companies. Utilising this platform will support your findings for upcoming projects, with over 200 members profiles showcasing the latest product launches, new materials available, industry news and design trends.