UK Made
Few of us appreciate how important manufacturing is to the UK economy. In September 2020 Make UK published a report highlighting UK’s position as the ninth leading manufacturer in the world with output totalling £191bn in 2019. The UK manufacturing sector employs around 2.7 million people with average wages 13% higher than the rest of the economy.
We caught up with John Pearce, CEO, Made in Britain (MiB), a not-for-profit dedicated to supporting British manufacturers, helping them sell more at home and abroad with the use of the official, protected Made in Britain mark. MiB’s membership is largely made up of SME’s who are seeing a big uptick in professional procurement centred on provenance and sustainability in 2021.
“Brexit and the pandemic have led to greater awareness of provenance and a new climate of public support for businesses that can prove it. We’ve seen a clear shift in attitudes, with more consumers and businesses more likely to buy more products made here. The sooner we buy more British-made products, the sooner we can rebuild better and greener in the post Brexit, post-pandemic economy” explains John Pearce, CEO, Made in Britain.
“One of the silver linings of a year full of uncertainty is being forced into seeing what can be created on our shores. There has been a noticeable, and rapid move away from a centralised to a more localised supply chain. One which serves to keep manufacturing as close to home as possible. Our industry has been for the most part ‘open for business’ and in the process proven itself to be productive and resilient”, he adds.
BCFA member, Roman has been designing and manufacturing showering solutions for over 36 years and is the UK’s largest shower manufacturer. As a privately owned family business with strong values and ethics, UK Made products are at the heart of everything they do.
David Osborne, CEO at Roman said, “There has never been a better time to be a British manufacturer and we are starting 2021 on nothing but positives – despite the ongoing pandemic surrounding us. As the largest manufacturer in our sector, we have always been strong advocates for Made in Britain – and very active within that organisation. In the post Brexit era, the real issue for the UK bathroom industry is the huge and ongoing increases in the cost of importing finished goods due to the knock on effects of COVID-19 on world shipping. Importers, suppliers and distributors of imported finished goods will be passing on unprecedented price increases into the market early in 2021.
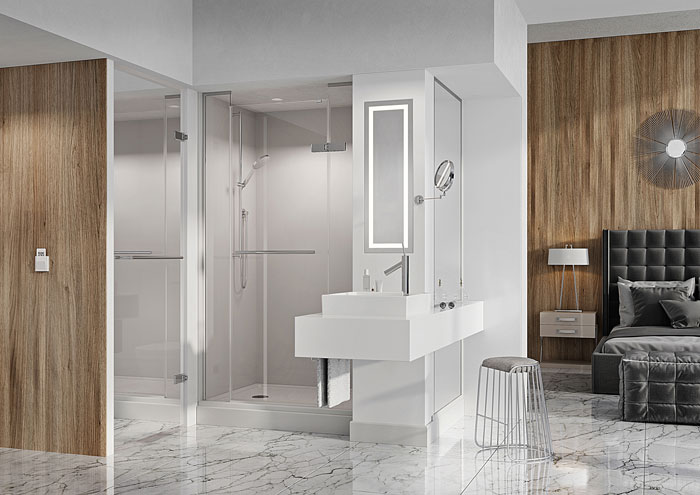
Roman shower enclosure, toilet with vanity unit made for Novotel (part of the Accor Group)
“The growing impact of carbon footprinting, the circular economy and sustainability is constantly growing in importance for Roman as a British manufacturer and is a clear differential against imported finished goods from China. Carbon footprinting is playing more on the minds of hotels and housebuilders, and moving higher up their purchasing agenda. In retail, if showrooms have never cared or even asked about product origin, it’s now obvious with the ongoing supply disruption from China which has forced retailers and housebuilders to re-evaluate their supply chains and product origin. The COVID-19 crisis has clearly made people ask questions about their supply chains; certainty of supply; product provenance; and seems to have renewed interest in British quality and ethics. From our own point of view and also from our key customers, we expect an extremely positive next 12-24 months, with strong growth in all channels especially the International export market for the Hotel and Hospitality sector.
“Over the last 10 years, the hospitality market has fast become one of our key focuses. We have constantly invested in and evolved our manufacturing capability and we now offer architects and designers a complete bespoke design and manufacturing service – wherever the project might be in the world. We have now supplied projects in over 60 countries worldwide and this is growing all the time.”
One of the key strengths of Ulster Carpets Group is their vertically integrated manufacturing structure in the UK, which provides complete control of every step of the process.
Ulster Carpets have been manufacturing in the UK since 1938 and their headquarters remain on the same site that the company was founded on. Supplying both the residential and contract markets, Ulster’s carpets feature in some of the world’s most prestigious hotels, casinos, and cruise ships around the world.
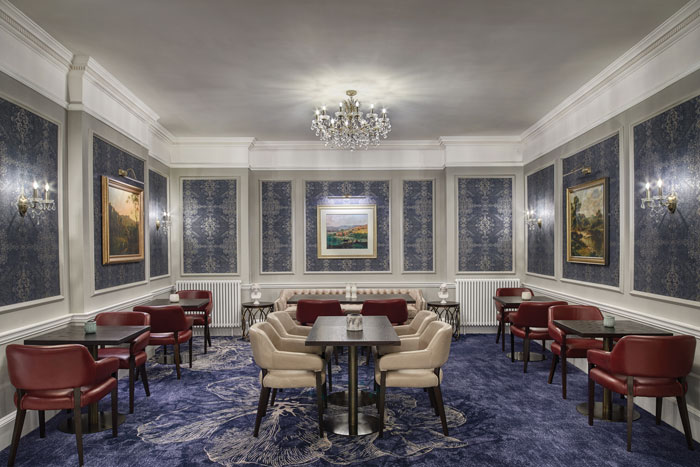
Bespoke Ulster Carpet in Buxton Crescent Hotel & Spa. Photography courtesy of Ensana Hotels.
Being owned and run by its founding family has allowed Ulster to implement a long-term strategic vision that has helped them to become the premier supplier of Axminster and Wilton carpets to the world market. Rather than be adversely affected by Brexit, the Northern Ireland Protocol has put them in a unique position as transactions in goods between Northern Ireland and EU businesses continue as they have in the past; that means no duties, checks on rules of origin or any barriers to movement within the EU Single Market.
In addition to their headquarters in Portadown, Ulster Yarns in Yorkshire and Ulster Carpets North East in Sunderland are part of a highly integrated manufacturing system. This allows control of every process, from sourcing the highest quality wool, including British Wool, and spinning and dyeing the yarn through to the bespoke design and weaving of the finest Axminster and Wilton carpets.
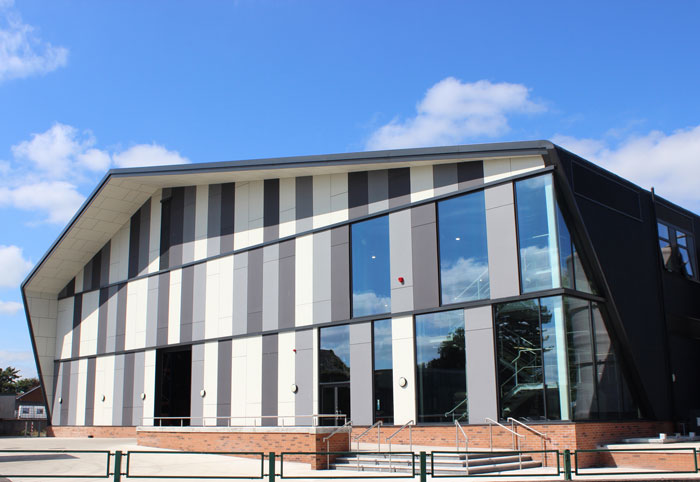
Ulster’s state-of-the-art Dyehouse & Energy Centre in Portadown, Northern Ireland.
Joyce McIvor, Contract Sales Director, UK and Ireland said, “We are very proud to have helped maintain the UK’s rich textile history. Around 75% of our carpet is exported outside the UK to hotels, casinos and cruise ships across the world but even with that global outlook, our focus remains on delivering a local service tailored to each customer’s needs.
“We work extensively on projects in the UK and also with UK designers working on projects across the world. With more pressure to get projects completed faster, our ability to meet deadlines while still delivering a quality product is a real advantage. We proved that during this pandemic, as we were able to successfully complete a wide range of different projects even with the various restrictions in place.”
Newmor Wallcoverings was established in 1967 and is proud to be family owned to this day. Operating in over 70 countries worldwide, it is the largest independent, privately owned, commercial wallcovering manufacturer in the UK. Over 90% of the wallcoverings they supply are designed and manufactured in their own facility in Welshpool.
Newmor specialise in commercial quality, wide-width fabric-backed vinyl wallcoverings. As well as manufacturing thousands of stocked designs, they also produce custom designed large format digital prints. It is their combination of traditional manufacturing alongside cutting-edge new technology that has resulted in the expansion of commission printing for brands who no longer manufacture in the UK.

Newmor Wallcoverings in Swift’s Whistler Lodge.
Whist some parts of the hospitality sector have taken the opportunity to refurbish, the majority of hotel projects have seen delays. However, Newmor’s agile approach to the changing customer demand has resulted in strong growth in the leisure sector as more people have holidayed in the UK. A trend which may well grow as consumers become more environmental conscious.
David Johnson, MD at Newmor said, “Being responsive to our customers changing needs sits at the heart of our business. We have been able to support the growing holiday lodge sector due to our short lead times. At the same time, we have developed new anti-microbial wallcoverings for use in healthcare and care home settings. Developing new products is a fundamental part of our business as we see potential demand for this additional level of protection without compromising on design style in commercial settings including hospitality.”
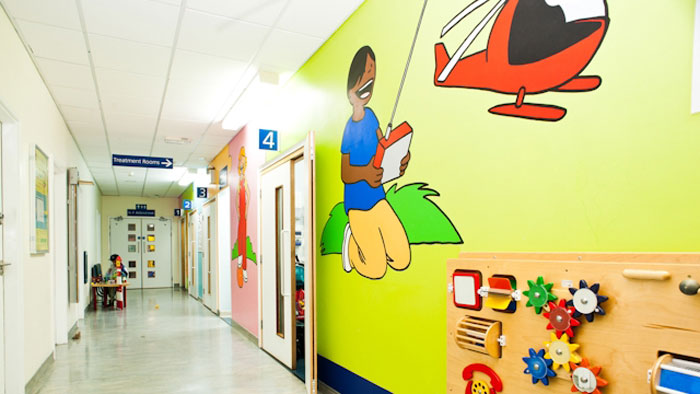
Newmor bespoke wallcoverings and window graphics at Birmingham Children’s Hospital.
Being UK Made has had distinct advantage at a time when supply chains are disrupted by a global pandemic and Brexit. It is interesting that the three BCFA members we interviewed are all family owned and have a longer term view on investment. Perhaps, something that other sectors in the UK can learn from.