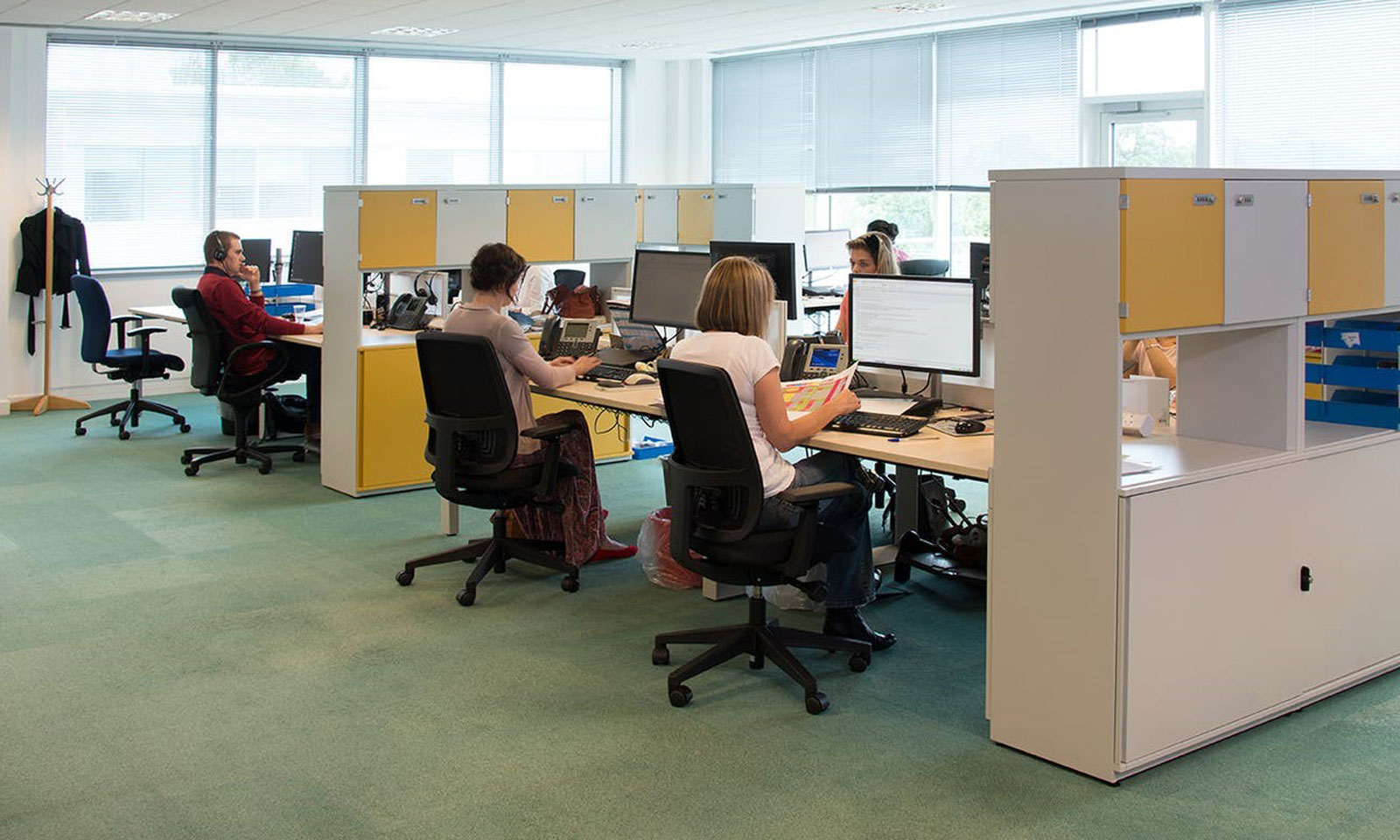
The effect of materials & processing technology on office development
Monthly Column By John Fogarty
Particleboard and the ability to produce it in large sheets – cut, shaped and edged in a wide variety of sizes and finishes – was perhaps the first significant and liberating breakthrough in materials processing to affect the development of office (and other) furniture design and production.
Veneered and lacquered post-primary-manufacturing finishes have over time been overwhelmingly replaced by pre-applied melamine surfaces; in a drive to simplify process and reduce the cost of manufacture and ownership. The cost of production has tumbled as variety and choice has increased.
Why then – as mentioned in my previous article – when I look at the latest postings on LinkedIn do I see piece after piece proudly flagging up the installation of yet another vast acreage of identical white-surfaced benches with black or grey leg frames? Is this at the insistence of Facilities Managers, who only see furniture as yet another readily interchangeable asset – or is it lazy and unimaginative Workplace Designers and Salespeople not making customers aware of the veritable cornucopia of choice available?
Whatever the case; when we know that staff blossom when given the freedom of free-range chickens, why do we insist on treating them like battery hens?
Sheet metal production, with particular application to office storage, is another area where the advance in materials and processing has had a significant positive effect on product development. CNC shaping and forming, welding and other assembly robotics and electrostatic finishing are the major areas where technology has delivered significant efficiency and cost benefits.
Smart Design and Engineering has moreover combined to produce end products that are as adaptable and flexible in their initial customer specification format as they are in later alternative use and re-use; thus imbuing them with the ultimate “green” credential of longevity.
Task seating is undeniably the area where the greatest advances in office furniture design have been made. Driven by a combination of far better understanding of anthropometric data, significant advances in polymer technology and the allocation of generous development and capital budgets, seating design has come on in leaps and bounds.
In Europe this development was pioneered by companies such as Vitra and Wilkhahn, while in the US the key players were Herman Miller, Steelcase, Knoll and Humanscale. Design was by named external designers, in collaboration with significant in-house Engineering teams.
The capital-intense products produced were spectacularly better than anything that had existed previously; employing as they did human measurement research, materials, mechanisms and manufacturing processes in ever more innovative, functional and stylish ways.
Having over time become somewhat over-laden with adjustment complexity, the most recent development direction has been towards simpler, self-adjusting products that rely on user weight and disposition to provide supportive, healthy seating posture.
There can be absolutely no employer excuse for poor seating provision in the current market.